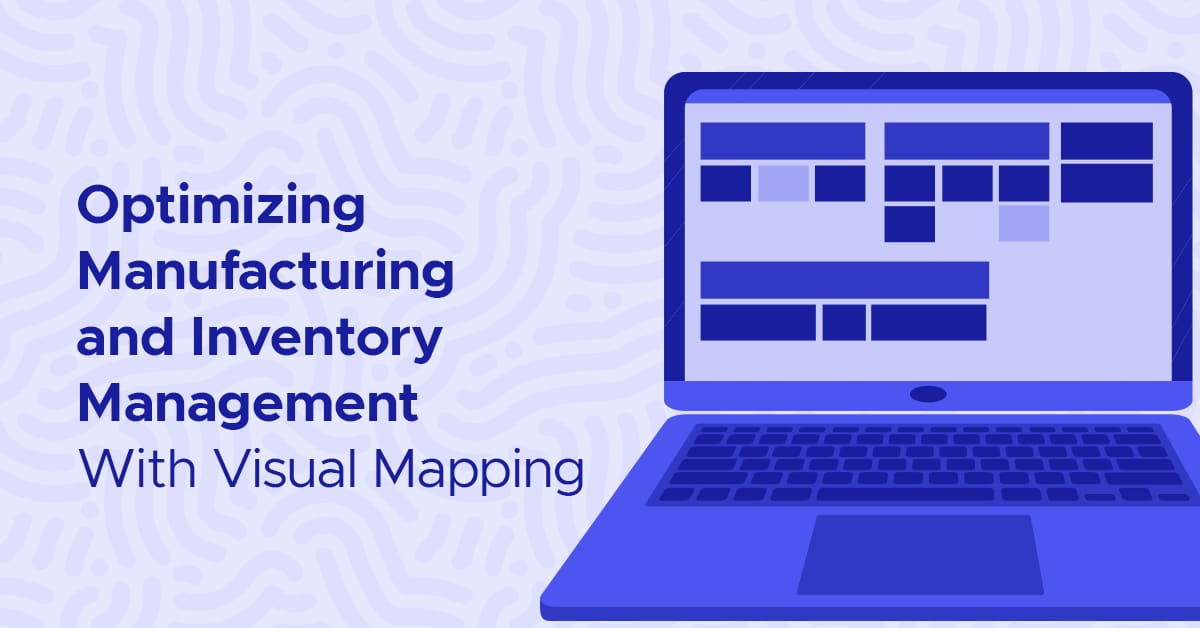
This is a guest post from Claude Rivera. Claude is a channel manager at CyberStockroom, where she specializes in empowering businesses to overcome the challenges of inventory management through innovative software solutions. With a focus on the needs of companies that manage field inventory, Claude and her team offer a robust SaaS platform designed to simplify and streamline inventory processes. Her dedication to assisting inventory managers and business owners comes from a deep understanding of the operational hassles they face daily.
Efficiency is crucial in manufacturing. Visual mapping is one of the largest benefits of inventory visibility and is a revolutionary solution rapidly gaining popularity in the industry.
Visual maps offer manufacturers an unparalleled level of insight into and control over their production processes and inventory. That includes tracking progress through each stage of manufacturing until the final products are ready to be stored in a warehouse or enter the supply chain.
This article will explain the benefits of inventory visibility and challenges of this innovative technology, as well as how to incorporate it into your own manufacturing business for more organized and streamlined production.
A warehouse map depicts the production floor, complete with workstations, storage areas, and paths for moving inventory in great detail.
With improved interdepartmental cooperation, rapid decision-making, and effective inventory management, this display significantly increases visibility throughout the whole manufacturing process.
A manufacturing demo map from CyberStockroom
Thanks to these real-time insights into inventory levels and movements, manufacturers can:
The benefits of inventory visibility also enable the easy identification of potential issues or inefficiencies in the manufacturing process.
By visualizing the flow of materials and goods through the production line, companies can quickly hone in on areas that require improvement, such as refining layout designs, adjusting inventory storage locations, or streamlining task flows.
In turn, this proactive approach helps manufacturers maintain responsiveness to changing market demands and supports higher productivity and profitability.
Visual map inventory management empowers businesses to gain a competitive edge by:
Incorporating visual map inventory management into manufacturing operations unlocks many advantages that improve productivity, accuracy, and overall performance.
Inventory maps provide a comprehensive view of stock levels for all items, including raw materials, work-in-progress, and finished goods.
That oversight allows for real-time monitoring, which facilitates better decision-making and optimal resource allocation.
Visual mapping of manufacturing processes and inventory locations can help companies streamline workflows.
That enables personnel to identify bottlenecks easily, optimize material flow, and reduce unnecessary movements, which then reduces cycle times and increases productivity.
Manufacturers can refine their inventory organization with visual maps based on demand, shelf life, and production requirements. This minimizes stockouts, overstocking, and obsolescence.
Manufacturers also gain a bird’s-eye view of their physical facility layout thanks to inventory visual maps. The benefits of inventory visibility helps them make the most of their available space and arrange inventory locations efficiently.
By optimizing storage configurations, companies can reduce wasted space, increase storage capacity, and quickly adjust to fluctuating inventory levels without needing more area. This enhances operations and reduces costs for greater efficiency.
Visual inventory maps can simplify the onboarding process for new employees as well as facilitate training for existing staff. These maps have clear and intuitive layouts that enable personnel to familiarize themselves quickly with inventory locations, production workstations, and processes. That significantly cuts down on the time and resources required for training initiatives.
Companies can introduce the benefits of inventory visibility into their operations through physical mapping and visualization software.
Physical mapping facilitates smooth operations in a manufacturing facility by clarifying visibility of the production floor. You can implement physical mapping through:
An inventory and manufacturing visual map is a graphical tool that represents a business’s daily operations. It depicts a manufacturing facility’s layout, showing the location of each manufacturing process, as well as how products and materials are distributed within the warehouse or facility.
Inventory map software is helpful for outlining manufacturing processes like receiving products, picking, packing, and logistics. Businesses can then follow the flow and record their everyday footprints.
Being able to detail inventory and manufacturing processes is a unique feature that’s not commonly found in most software but is highly sought after due to its potential to boost stock visibility and operational efficiency.
Using an inventory map enables you to locate items in your storehouse quickly, reduces the time it takes to pick and pack orders, and optimizes your warehouse layout.
The benefits of inventory visibility play a pivotal role in modern manufacturing facilities. The visual maps provide a clear and intuitive representation of the entire production process.
Here’s a comprehensive look at how manufacturers can introduce visual maps to hone their operations:
Various challenges and potential pitfalls can arise in the implementation of inventory visibility management. However, manufacturing businesses can introduce this method into their operations with minimal friction by taking proactive measures and applying best practices.
Below are the typical problems encountered and some suggested solutions:
As manufacturing evolves, new technologies and practices are shaping the industry’s future. Here are some notable trends and innovations that could benefit from the application of visual mapping:
The benefits of inventory visibility include greatly aiding the management of a factory or manufacturing business. They outline what occurs in a facility and help you identify and address problems before they escalate.
With the support of that real-time information, you can make informed decisions that save time and improve productivity, including:
By adopting visual maps, factories and manufacturing businesses reap the benefits of inventory visibility by becoming more agile and adaptable to the ever-changing market. That, in turn, improves operational efficiency and long-term sustainability.