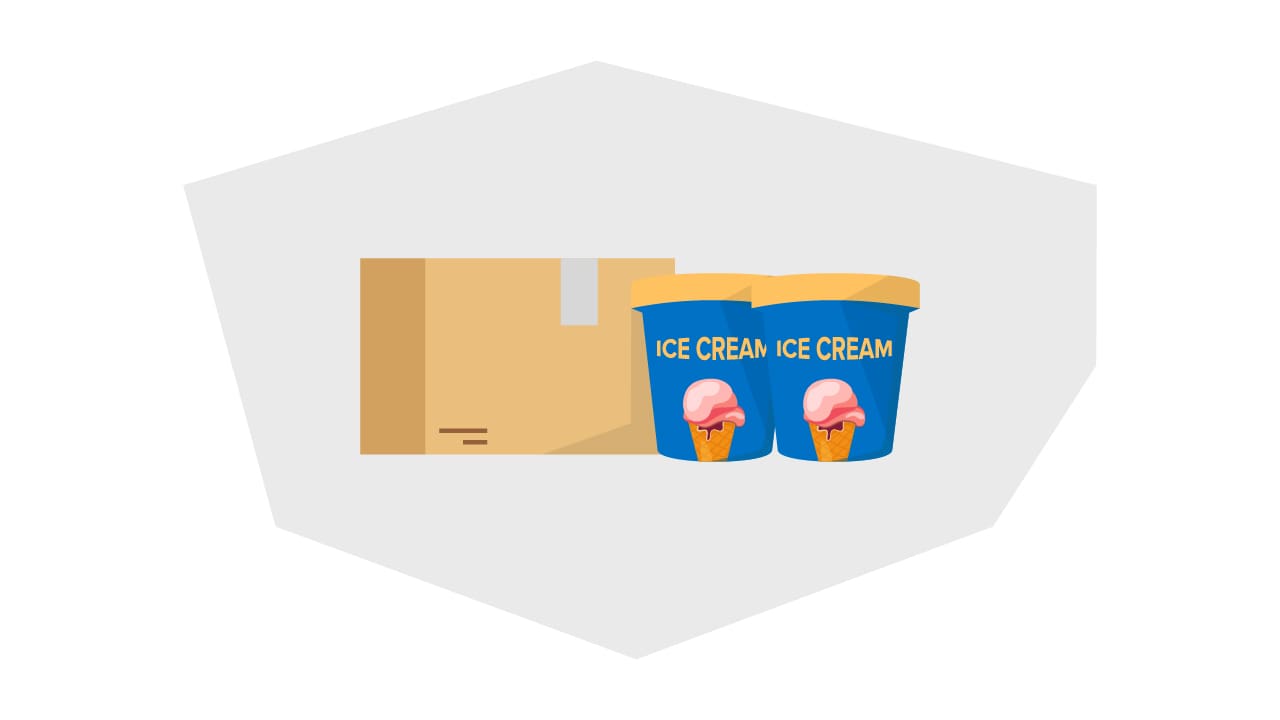
From the rise of online groceries to food subscription boxes and increasing vegetable imports from Mexico, cold chain logistics is on the rise. That trend affects thousands of eCommerce sellers, who are seeing an increasing demand for the convenience of ordering food online. However, it introduces new challenges to logistics as well in the form of cold chain shipping.
Tackling the intricacies of cold chain logistics can be daunting — so much so that some 3PLs avoid it entirely. However, in industries such as food, beverages, and biopharmaceuticals, mastery of cold storage prep and shipping is a necessity. We’ll walk you through the basics of these complexities and how to navigate them to ensure your temperature-sensitive goods are handled professionally and efficiently.
Cold chain logistics is the storage and distribution of goods at a controlled temperature. It typically entails food and other perishable goods but can also mean transporting any other such goods like makeup, perfume, flowers, medicine, candles, and even artwork. If your goods are temperature sensitive, you’ll need cold chain logistics to move them through areas that could otherwise damage the products.
Temperature-sensitive goods must remain within a certain temperature range to ensure quality, freshness, and safety, and logistics are a key breaking point. Often, cold chain products also require shifts in delivery frequency as well. For example, it’s common to adopt a strategy of small shipments with short delivery times to enable storage capacity and the ability to keep products cold during transit. This is why a reliable cold chain shipping strategy is essential.
The cold chain process generally incorporates additional considerations compared to traditional shipping, like:
Shippers and third-party logistics (3PL) providers continuously adapt to consumers, and that includes cold chain shipping: NTT Data’s 2023 27th Annual Third-Party Logistics Study found 67% of shippers and 72% of 3PLs are expanding their cold chain capabilities and capacity over the next three years. It’s further anticipated that, by 2030, the global chain logistics market will reach about $801.26 billion and grow at a CAGR of 14.07% from 2022 to 2030.
Two increasingly influential industries, grocery delivery and micro-fulfillment, are contributing to this expansion as they broaden their logistical capabilities to include cold chain shipping.
eCommerce and online grocery services are gaining a larger share of the cold chain industry. Over the next five years, online grocery sales will see a CAGR of 11.7%, bumping eCommerce’s share of overall grocery spending from 11.2% in 2022 to 13.6% in 2027.
This trend will continue as customers are now used to the convenience and time savings of grocery delivery. Moreover, by 2026, eCommerce is predicted to take up 20% of the U.S. grocery industry.
While this growth is exciting, grocery retailers feel pressured to deliver products to customers quickly while meeting increasing demands. To support service deliveries and operations, brick-and-mortar stores now look to cold chain shipping for guaranteed food freshness. eCommerce brands also have to consider aspects of fulfillment like:
Micro-fulfillment involves establishing smaller-scale warehouses in populous urban or suburban locations. By shortening the physical distance between consumers and goods, businesses reduce their last-mile delivery time. This is especially important to the cold chain, as it improves supply chain efficiency and lowers the costs and risks associated with temperature-sensitive shipments.
Micro-fulfillment centers typically carry enough stock to cover a few days’ worth of orders. They rely heavily on inventory management software and customer-driven analytics to determine what SKUs are most often purchased, by which customers, and in what geographic areas. This ensures product availability and eliminates wasted storage and stagnant inventory.
It also allows those storage points to maintain stock without overloading cooling resources such as refrigerators and freezers. However, it does require business to align deliveries carefully with throughput and expected sales to avoid stockouts and lost income.
Thanks to modern advancements, companies can track shipments live, which includes the ability to view real-time temperature and adjust it dynamically based on outside conditions. Even AI and machine learning now offer analytical tools that use data to help keep products at an optimal temperature throughout their journey. That also yields actionable insights like predicted inventory, transportation time, consumer demand, and spoilage probability.
Software products can also monitor the trailers used during transportation between distribution centers to ensure temperatures remain consistent. Previously, cold chain shipping employed passive temperature sensors — battery-powered thermometers that would monitor the food containers rather than the trailers. However, new technologies allow products to ship in ideal temperature conditions as well as provide live data on temperature fluctuations.
Adopting Bluetooth low-energy (BLE) trackers, for example, enables users to monitor the temperature and climate of transportation containers remotely with real-time insights like humidity, movement, data entry, and analytics. This reveals any issues concerning suboptimal conditions that businesses can improve with GPS, RFID, and barcodes.
If goods arrive spoiled, it can be difficult to pinpoint where the breakdown occurred without sophisticated software. Advanced tracking systems continuously track temperature and humidity to alert users if pre-configured limits are breached, thus proactively preventing damage. Often, location-based insights like GPS will inform you where the goods are when they’re damaged. This helps you trace the timeline back to ensure accountability and avoid repeating these mistakes.
A recent Forbes study found 61% of shippers outsource cold storage and warehousing to some degree. This is primarily due to the significant costs of investing in and maintaining temperature-controlled logistics, which includes special equipment and established processes for temperature-sensitive items.
Shelf life and temperature ranges can vary drastically from product to product. They usually fall into two main segments: chilled and frozen goods. However, items can fall anywhere within that range, making it impossible to keep everything at a single, uniform temperature. You must establish a process for keeping track of acceptable temperature ranges to reduce waste and regulate temperatures 24/7. That’s true even if you ship items with different temperature requirements (e.g., meat and produce alongside frozen goods).
Complying with local, state, and federal safety regulations is crucial for preserving the safety and quality of perishable goods. One such statute is the Food Safety Modernization Act (FSMA), which requires shippers to complete temperature reports and maintain documented sanitary practices.
New regulations are proposed all the time, so be sure to check them regularly to stay up to date and in compliance. Working with a 3PL brings experts who manage compliance for you, which can save considerable headache, especially when it comes time to report or cooperate with an audit.
The type of storage you use has a massive impact on the quality of cold goods. You can choose from various refrigeration equipment like refrigerated containers, blast freezers, cold rooms, or pharmaceutical-grade cold storage. The goal is to keep temperatures consistent and prevent exposure to outside elements, so do your research to select the right type of unit for your cold goods.
Packaging cold storage items requires great care, as mishandling can lead to diminished product quality or spoilage. The greatest challenge at this stage is ensuring temperatures stay within an acceptable range and preventing external factors like humidity from ruining the item. Give careful attention to the following elements:
Aside from securing your products, you must also account for possible leakage and perspiration. Double-bagging, absorbent pads, or cellulose wadding can help combat those potentialities.
If you sell on third-party marketplaces like Amazon, you may also be required to provide information like the shipper’s name and the location where the contents were grown or manufactured.
The rise in global trade and demand for perishable goods has increased the importance of reliable cold chain shipping in recent years. This logistical niche is essential to ensure perishable products are delivered safely and on time.
Shipping temperature-sensitive goods with cold chain shipping is essential for improved safety, extended shelf life, reduced waste, and cost savings on products. Most importantly, it reduces the risk of spoilage due to temperature fluctuations, which can cause serious health issues or even product recalls.
By controlling the temperature and humidity of the product environment, cold chain shipping allows items to be transported over longer distances without compromising quality. This helps businesses maintain inventory levels more effectively, as well as ensures products reach their destination on time and in perfect condition.
Shipping cold and frozen goods poses substantial challenges. Even with perfect packaging and storage, improper shipping methods can lead to unhappy customers and lost revenue. So, before you ship your products, you must develop a dependable strategy, ensure your technology is up to scratch, and establish a process to monitor those procedures. Key components to hone are:
An increasingly popular way to tackle these cogs in the cold chain machine is to outsource the process to a 3PL. In fact, 72% of cold storage in the U.S. is now outsourced. Often, it makes more sense for organizations to invest in a third-party service that can provide existing infrastructure, rather than building and maintaining that infrastructure themselves.
Cold chain shipping is prone to issues and headaches. You can avoid these problems though and ensure well-oiled operations by adhering to best practices.
Or, you can take advantage of a 3PL’s connections, like MyFBAPrep. We collaborate with these and other reliable carriers to obtain the best rates for clients. You’ll also enjoy optimized shipping times so your temperature-sensitive goods reach their destination safely and promptly.
With cold chain shipping increasing in usage, 3PLs are also expanding their cold chain management services. As such, more and more retailers want to outsource their cold chain warehousing and distribution to encourage their business growth. Because it requires specialized labor, warehousing, and transportation, a 3PL with experience and expertise in managing sensitive products can save brands significant costs.
When looking at 3PL providers, it’s important to evaluate:
If your brand’s growth is dependent on incorporating cold chain shipping, you need to dedicate time and energy into either perfecting your logistics or finding a great 3PL partner to handle it for you. Cold chain shipping will continue to corner the market as consumer preferences fluctuate due to the introduction of new products and brands. Take advantage of this growth to expand your brand and achieve greater success (and revenue).
Temperature-controlled logistics is complicated terrain. These types of deliveries are always on a time crunch, so you need tight planning for your packaging, timing, and routes — otherwise, you could end up with ruined goods that cost you revenue and erode your business reputation. However, you can remove some of that headache with MyFBAPrep’s comprehensive solutions and team of dedicated experts. From regulatory compliance to perfect packaging, we have you covered.
Published: June 12, 2023
Updated: July 8, 2024