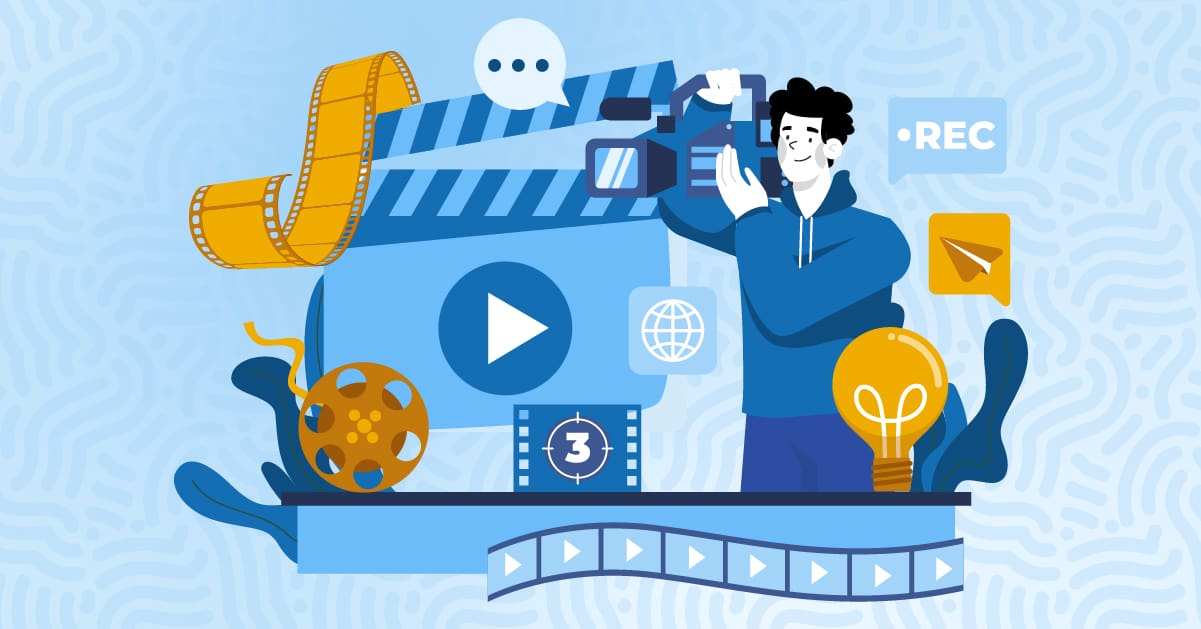
This is a guest post from VisAI Labs, which provides packaging station monitoring tools that can automatically log state of packages, dimensions, and more during the pick/pack/ship process.
A customer opens their package expecting everything to be perfect, only to realize a key item is missing. Frustrated, they contact support, and your team or 3PL partner struggles to pinpoint what went wrong. Sound familiar?
In the era of two-day delivery windows, even the smallest mistake at the packing station can create a ripple effect and lead to returns, dissatisfied customers, and unnecessary disputes between fulfillment partners. For eCommerce retailers and 3PLs alike, the consequences of an incorrect order are increasingly steep.
One in a hundred packages has a packing error, such as a missing item, wrong product, or bad packaging, and each of those can easily cost you over $50 in costs for labor, reshipping, and refunds. Returns further complicate matters: A recent study from Apprises Retail and Deloitte found that, in 2024, retailers lost $103 billion due to fraudulent returns and claims.
Most warehouses rely on some form of CCTV or physical check to identify packing issues, but neither of those methods provide visual evidence to dispel all doubt when a dispute arises. Fulfillment centers need visual intelligence to hone in on packing errors, which entails adopting tools like vAudit Video Logger.
Below are six ways video logs can transform your packing station into a hub of clarity, efficiency, and operational trust. In turn, you’ll see a measurable impact on your quality assurance teams, customer support, and operations managers.
A major challenge in fulfillment is pinpointing where an error has occurred (e.g., was it an issue with packing or shipping?). It’s almost impossible to determine with CCTV because the video quality doesn’t allow you to view individual items.
vAudit solves this problem by recording 4K resolution video for every order packed and tagged with the order ID. So, when an issue arises, you can find the video with the click of a button and jump to see how the order was packed.
For example, when you look at the video and see your team packed the order correctly, then most likely the error happened during shipment. Or, if the mistake did occur at the packing station, it can be resolved immediately.
Fulfillment errors (like shipping the wrong item, omitting a SKU, or packing too many items) are only realized after the order has been delivered to the customer, requiring a return or complaint.
Standard practices like manual checks and packing slips are helpful, but they won’t eliminate the error risk. In most cases, they don’t detect problems proactively.
vAudit offers capabilities to prevent the risk of errors at the packing stage. While traditional approaches can attempt verification, vAudit verifies every item in an order using barcodes. This occurs in real time to identify mismatches and missing items, then the system alerts the packer before the box is sealed and shipped.
Customers may report missing or damaged items or send back entirely different products. Fulfillment centers and 3PL providers often default to a refund in cases where a buyer claims their shipment was wrong because they have no visual evidence of what was in the original pack.
With the help of vAudit’s video logging solution though, you can capture high-quality video of each order at the point of packing to summarize product conditions, item quantities, and packing method.
Once a return is started, you can instantly compare the returned item to the original video of what was shipped to quickly identify false claims.
If the return doesn’t match what was packed, you can flag the claim, while if you find the product sent back does match, you can process the claim faster.
Every claim has a cost — sometimes more than just money. If the company can’t prove what was packed, refunding the customer is usually the go-to (even when the order was packaged correctly). These payouts can add up fast, especially when they include missing item claims, incorrect product claims, etc.
To avoid these unnecessary expenses, vAudit verifies each order by checking the automated barcodes and 4K video captured before they leave the packing station.
Even with standard operating procedures (SOPs), accuracy declines as the volume of orders grows. Missed items, wrong SKUs packed, and excess packaging can lead to more returns, acceptable tickets, and lost trust.
By validating each item in real time while capturing 4K video of every order packed, vAudit gives your teams full procedural visibility to hone in on trends, address ongoing issues, and ensure accurate shipments.
Today’s consumers want more than just fast delivery — they want transparency. By making packing videos available to support teams (or directly to customers when appropriate), brands can demonstrate precisely how each order is assembled.
When consumers know which products are included in orders or how they were packed, this added visibility establishes trust and reduces frustration.
In an environment where speed is expected and accuracy is taken for granted, visibility is no longer optional. Building visual intelligence into the packing process allows teams to make quicker decisions, troubleshoot with clarity, and build more confidence at every level of operations.
See how video-backed visibility can transform your fulfillment workflow, whether you manage in-house operations or partner with a 3PL.